Fúrólyuk vegyi befecskendező vezetékek – Miért hibáznak?Új vizsgálati módszerek tapasztalatai, kihívásai és alkalmazása
Copyright 2012, Society of Petroleum Engineers
Absztrakt
A Statoil több olyan mezőt is üzemeltet, ahol vízkőgátló fúrólyukba történő folyamatos befecskendezését alkalmazzák.A cél az, hogy megvédje a felső csövet és a biztonsági szelepet a (Ba/Sr) SO4 vagy CaCO ellen;léptékben, azokban az esetekben, amikor a vízkő leszorítása nehéz és költséges lehet rendszeresen végrehajtani, pl. tenger alatti mezők összekapcsolása.
A vízkőgátló fúrólyuk folyamatos befecskendezése műszakilag megfelelő megoldás a felső csővezeték és a biztonsági szelep védelmére azokban a kutakban, amelyekben vízkőlerakódási potenciál van a termelési csomagológép felett;különösen azokban a kutakban, amelyeket nem kell rendszeresen kinyomni a kút közelében lévő vízkőlerakódás miatt.
A vegyszerinjektáló vonalak tervezése, üzemeltetése és karbantartása fokozott figyelmet igényel az anyagválasztásra, a vegyszerminősítésre és az ellenőrzésre.A nyomás, a hőmérséklet, az áramlási viszonyok és a rendszer geometriája kihívásokat jelenthet a biztonságos működésben.Kihívások merültek fel a több kilométer hosszú befecskendezési vonalakban, amelyek a gyártólétesítménytől a tenger alatti sablonig tartanak, és a kutak befecskendező szelepeiben.
Megvitatják azokat a helyszíni tapasztalatokat, amelyek a fúrólyuk folyamatos befecskendező rendszerek összetettségét mutatják csapadék- és korróziós problémákkal kapcsolatban.Laboratóriumi vizsgálatok és új módszerek alkalmazása a kémiai minősítésre a.A multidiszciplináris fellépések szükségleteit kielégítik.
Bevezetés
A Statoil több olyan mezőt üzemeltet, ahol fúrólyuzatos folyamatos vegyszer-injekciót alkalmaztak.Ez főleg vízkőgátló (SI) befecskendezését foglalja magában, ahol a cél a felső csővezeték és a biztonsági szelep (DHSV) védelme a (Ba/Sr) SO4 vagy CaCO ellen;skála.Egyes esetekben az emulziótörőt a fúrólyukba fecskendezik be, hogy az elválasztási folyamat a lehető legmélyebben, viszonylag magas hőmérsékleten elinduljon a kútba.
A vízkőgátló fúrólyuk folyamatos befecskendezése műszakilag megfelelő megoldás a kutak felső részének védelmére, amelyek a termelési csomagoló felett vízkőlerakódási potenciállal rendelkeznek.A folyamatos befecskendezés különösen azokban a kutakban javasolt, amelyeket nem kell összenyomni, mivel a közeli kútfúrásban alacsony a vízkőképződés;vagy olyan esetekben, amikor a vízkőlenyomat rendszeres végrehajtása nehézkes és költséges lehet, pl. tenger alatti mezők összekapcsolása.
A Statoil kiterjedt tapasztalattal rendelkezik a folyamatos vegyszerinjektálás terén a felső rendszerekhez és a tenger alatti sablonokhoz, de az új kihívás az, hogy a befecskendezési pontot még mélyebbre vigye a kútba.A vegyszerinjektáló vezetékek tervezése, üzemeltetése és karbantartása több témára is fokozott figyelmet igényel;mint például az anyagválasztás, a kémiai minősítés és a monitoring.A nyomás, a hőmérséklet, az áramlási viszonyok és a rendszer geometriája kihívásokat jelenthet a biztonságos működésben.Kihívások merültek fel a hosszú (több kilométeres) befecskendező vezetékekben a termelési létesítménytől a tenger alatti sablonig és a kutak befecskendező szelepeibe;1. ábra.A befecskendező rendszerek egy része a terveknek megfelelően működött, míg mások különböző okok miatt meghibásodtak.Számos új terepfejlesztést terveznek a fúrólyukú vegyszerinjektálás (DHCI) területén;azonban;egyes esetekben a berendezés még nem teljesen minősített.
A DHCI alkalmazása összetett feladat.Ez magában foglalja a befejezést és a kúttervezést, a kút kémiáját, a felső oldali rendszert és a kémiai adagolási rendszert.A vegyszert a felső oldalról a vegyszerinjektáló vezetéken keresztül a befejező berendezésbe és le a kútba pumpálják.Ezért az ilyen típusú projektek tervezésében és lebonyolításában kulcsfontosságú a több szakterület közötti együttműködés.Különféle szempontokat kell értékelni, és fontos a jó kommunikáció a tervezés során.Folyamatmérnökök, tenger alatti mérnökök és befejező mérnökök vesznek részt, akik a kútkémia, az anyagkiválasztás, az áramlásbiztosítás és a termelési vegyszer-menedzsment témaköreivel foglalkoznak.A kihívások lehetnek a vegyi pisztolykirály vagy a hőmérséklet-stabilitás, a korrózió és bizonyos esetekben a vákuumhatás a helyi nyomás és áramlási hatások miatt a vegyszerinjektáló vezetékben.Ezeken kívül olyan körülmények, mint a magas nyomás, magas hőmérséklet, nagy gázsebesség, nagy vízkőképződési potenciál,nagy távolságú köldök és mély befecskendezési pont a kútban, különböző technikai kihívásokat és követelményeket támaszt a befecskendezett vegyszerrel és a befecskendező szeleppel szemben.
A Statoil üzemben telepített DHCI rendszerek áttekintése azt mutatja, hogy a tapasztalatok nem mindig voltak sikeresek. 1. táblázat. A befecskendezési tervezés, a vegyszerminősítés, az üzemeltetés és a karbantartás fejlesztésének tervezése azonban folyamatban van.A kihívások területről területre változnak, és a probléma nem feltétlenül az, hogy maga a vegyszerbefecskendező szelep nem működik.
Az elmúlt években számos kihívást tapasztaltak a fúrólyuk vegyszer-injektáló vezetékekkel kapcsolatban.Ebben a cikkben ezekből a tapasztalatokból mutatunk be néhány példát.A cikk a DHCI vonalakkal kapcsolatos problémák megoldására irányuló kihívásokat és intézkedéseket tárgyalja.Két esettörténetet közölnek;egy a korrózióról és egy a vegyifegyver-királyról.Megvitatják azokat a helyszíni tapasztalatokat, amelyek a fúrólyuk folyamatos befecskendező rendszerek összetettségét mutatják csapadék- és korróziós problémákkal kapcsolatban.
A laboratóriumi vizsgálatok és a kémiai minősítés új módszereinek alkalmazása is számításba jön;a vegyszer szivattyúzása, vízkőlerakódási potenciál és megelőzés, komplex berendezések alkalmazása és a vegyszer milyen hatással lesz a felső rendszerre a vegyszer visszatermelése során.A vegyszerek alkalmazására vonatkozó elfogadási kritériumok környezetvédelmi kérdéseket, hatékonyságot, felső tárolókapacitást, szivattyúzási sebességet, használható-e a meglévő szivattyú stb. és e vonalak környezetében található anyagok.Előfordulhat, hogy a vegyszert hidráttal kell gátolni, hogy megakadályozzuk a befecskendező vezeték eltömődését a gáz inváziója miatt, és a vegyszer nem fagyhat meg szállítás és tárolás során.A meglévő belső irányelvekben van egy ellenőrző lista arról, hogy mely vegyszerek alkalmazhatók a rendszer egyes pontjain. Fontosak a fizikai tulajdonságok, például a viszkozitás.A befecskendező rendszer 3-50 km távolságot jelenthet a köldök alatti áramlási vonaltól és 1-3 km-t a kútba.Ezért a hőmérséklet stabilitása is fontos.Megfontolandó a downstream hatások értékelése is, pl. a finomítókban.
Fúrólyuk vegyszerbefecskendező rendszerek
Költség-haszon
A vízkőgátló fúrólyuk folyamatos befecskendezése a DHS védelmére Vor a gyártócsövek költséghatékonyabbak lehetnek a kút vízkőgátlóval történő összenyomásához képest.Ez az alkalmazás csökkenti a képződés károsodásának lehetőségét a vízkőpréseléses kezelésekhez képest, csökkenti a vízkő összenyomódása utáni folyamatproblémák lehetőségét, és lehetőséget ad a vegyszerinjektálás sebességének szabályozására a felső oldali befecskendező rendszerből.A befecskendező rendszer más vegyi anyagok folyamatos befecskendezésére is használható a lyukba, és ezáltal csökkentheti az egyéb kihívásokat, amelyek a feldolgozó üzemben később jelentkezhetnek.
Átfogó tanulmány készült az Oseberg S vagy mező fúrási léptékű stratégiájának kidolgozására.A legnagyobb méretű probléma a CaCO volt;pikkelyképződés a felső csőben és lehetséges DHSV-hiba.Az Oseberg S vagy a méretezési stratégia megfontolások arra a következtetésre jutottak, hogy három év alatt a DHCI volt a legköltséghatékonyabb megoldás azokban a kutakban, ahol a vegyszerinjektáló vezetékek működtek.A vízkőpréselés versengő technikája tekintetében a fő költségelem a halasztott olaj volt, nem pedig a vegyi/működési költség.A vízkőgátló alkalmazásánál a gázemelésben a vegyszerköltség fő tényezője a magas gázemelési sebesség volt, ami magas SI-koncentrációt eredményezett, mivel a koncentrációt egyensúlyba kellett hozni a gázemelés sebességével, hogy elkerüljük a vegyi pisztolykirályt.Az Oseberg S két kútja esetében, amelyek jól működő DHC I vezetékekkel rendelkeztek, ezt a lehetőséget választották a DHS V-k CaCO elleni védelmére;méretezés.
Folyamatos befecskendező rendszer és szelepek
A folyamatos vegyszer-injektáló rendszereket használó, meglévő befejezési megoldások kihívásokkal néznek szembe a kapillárisvezetékek eltömődésének megakadályozása érdekében.A befecskendező rendszer jellemzően egy 1/4” vagy 3/8” külső átmérőjű (OD) kapilláris vezetékből áll, amely egy felületi elosztócsőhöz van csatlakoztatva, át van vezetve és csatlakoztatva van a cső gyűrűs oldalán lévő csőakasztóhoz.A kapilláris vezeték a gyártócső külső átmérőjéhez speciális csőgallér-bilincsekkel van rögzítve, és a cső külső oldalán fut le egészen a vegyszerinjektáló tüskéig.A tüskét hagyományosan a DHS V előtt vagy mélyebben helyezik el a kútban azzal a szándékkal, hogy a befecskendezett vegyszer elegendő diszperziós időt biztosítson, és a vegyszert ott helyezze el, ahol a kihívásokat találják.
A vegyszerbefecskendező szelepnél (2. ábra) egy körülbelül 1,5” átmérőjű kis patronban vannak a visszacsapó szelepek, amelyek megakadályozzák a kútfolyadékok bejutását a kapilláris vezetékbe.Egyszerűen egy rugón lovagló kis láda.A rugóerő beállítja és megjósolja azt a nyomást, amely ahhoz szükséges, hogy a tömítőfülkét kinyissa.Amikor a vegyszer folyni kezd, a szelepszár felemelkedik az ülésről, és kinyitja a visszacsapó szelepet.
Két visszacsapó szelep felszerelése szükséges.Az egyik szelep az elsődleges gát, amely megakadályozza, hogy a fúrólyuk folyadékok bejussanak a kapilláris vezetékbe.Ennek viszonylag alacsony nyitási nyomása van (2-15 bar). Ha a hidrosztatikus nyomás a kapilláris vezetéken belül kisebb, mint a fúrólyuk nyomása, a fúrólyuk folyadékok megpróbálnak bejutni a kapilláris vezetékbe.A másik visszacsapó szelep atipikus nyitási nyomása 130-250 bar, és U-csöves gátló rendszerként ismert.Ez a szelep megakadályozza, hogy a kapilláris vezetéken belüli vegyszer szabadon beáramoljon a fúrólyukba, ha a kapilláris vezetéken belüli hidrosztatikus nyomás nagyobb, mint a fúrólyuk nyomása a vegyszer befecskendezési pontján a gyártócső belsejében.
A két visszacsapó szelepen kívül általában van egy soron belüli szűrő, ennek az a célja, hogy semmiféle törmelék ne veszélyeztesse a visszacsapó szeleprendszerek tömítőképességét.
A leírt visszacsapó szelepek mérete meglehetősen kicsi, működésükhöz elengedhetetlen a befecskendezett folyadék tisztasága.Úgy gondolják, hogy a rendszerben lévő törmeléket a kapillárisvezetéken belüli áramlási sebesség növelésével el lehet öblíteni, így a visszacsapó szelepek szándékosan kinyílnak.
Amikor a visszacsapó szelep kinyílik, az áramlási nyomás gyorsan csökken, és tovább terjed a kapilláris vezetéken, amíg a nyomás ismét meg nem nő.A visszacsapó szelep ezután zár, amíg a vegyszerek áramlása elegendő nyomást nem hoz fel a szelep kinyitásához;az eredmény nyomásingadozások a visszacsapó szeleprendszerben.Minél nagyobb a nyitási nyomás a visszacsapó szeleprendszerben, annál kisebb az áramlási terület, amikor a visszacsapó szelep nyit, és a rendszer megpróbál egyensúlyi feltételeket elérni.
A vegyszerbefecskendező szelepek nyitási nyomása viszonylag alacsony;és ha a csőnyomás a vegyszer bemeneti pontján kisebb lesz, mint a kapillárisvezetéken belüli vegyszerek hidrosztatikus nyomásának és a visszacsapó szelep nyitási nyomásának összege, a kapillárisvezeték felső részén vákuum vagy vákuum közeli állapot lép fel.Amikor a vegyszer befecskendezése leáll, vagy a vegyszer áramlása alacsony, a kapillárisvezeték felső szakaszában vákuumhoz közeli állapotok kezdődnek.
A vákuum szintje függ a fúrólyuk nyomásától, a kapillárisvezetéken belüli befecskendezett vegyszerkeverék fajsúlyától, a visszacsapó szelep nyitási nyomásától a befecskendezési ponton és a vegyszer áramlási sebességétől a kapilláris vezetékben.A kút körülményei a mező élettartama során változnak, és ezért a vákuum lehetősége is változni fog az időn túl.Fontos, hogy tisztában legyünk ezzel a helyzettel, hogy megfelelő figyelmet és elővigyázatosságot tegyünk, mielőtt a várható kihívások bekövetkeznének.
Az alacsony befecskendezési sebességgel együtt az ilyen típusú alkalmazásokban használt oldószerek jellemzően elpárolognak, és olyan hatásokat okoznak, amelyeket még nem tártak fel teljesen.Ezek a hatások a pisztolykirály vagy szilárd anyagok, például polimerek kiválása, amikor az oldószer elpárolog.
Továbbá galvanikus cellák alakíthatók ki a vegyszer folyadékfelülete és a fenti, gőzzel töltött vákuumközeli gázfázis közötti átmeneti fázisban.Ez helyi pontkorrózióhoz vezethet a kapilláris vonalon belül, a vegyi anyag fokozott agresszivitása következtében ilyen körülmények között.A kapillárisvonal belsejében filmként képződő pelyhek vagy sókristályok, ahogyan a belsejében kiszárad, elakadhatnak vagy eltömíthetik a kapillárisvezetéket.
Nos barrier filozófia
A robusztus kútmegoldások tervezésekor a Statoil megköveteli, hogy a kútbiztonság mindenkor a helyén legyen a kút életciklusa során.Így a Statoil megköveteli, hogy két független kútsorompó sértetlen legyen.A 3. ábra egy atipikus kútgát vázlatát mutatja, ahol a kék szín az elsődleges kútgát-burkot jelöli;ebben az esetben a gyártócső.A piros szín a másodlagos gátburkot jelöli;a burkolat.A vázlat bal oldalán a vegyszerinjektálás fekete vonalként van jelölve, a befecskendezési ponttal a gyártócsőhöz a pirossal jelölt területen (másodlagos gát).A vegyszeres befecskendező rendszerek kútba történő bevezetésével mind az elsődleges, mind a másodlagos fúrólyuk gátja veszélybe kerül.
Korróziós esettörténet
Az események sorrendje
A Norvég kontinentális talapzaton lévő Statoil által üzemeltetett olajmezőre vízkőgátló fúrólyukba fecskendeztek be.Ebben az esetben az alkalmazott vízkőgátlót eredetileg felső és tenger alatti alkalmazásra minősítették.A kút újbóli befejezését követte a DHCIpointat2446mMD telepítése, 3. ábra.A felső oldali lerakódásgátló fúvókás befecskendezését a vegyszer további tesztelése nélkül kezdték meg.
Egy év üzemelés után szivárgást észleltek a vegyszerinjektáló rendszerben, és megkezdődtek a vizsgálatok.A szivárgás káros hatással volt a kútkorlátokra.Hasonló események több kútnál is előfordultak, és néhányat be kellett zárni a vizsgálat ideje alatt.
A gyártócsövet kihúzták és részletesen tanulmányozták.A korróziós támadás a cső egyik oldalára korlátozódott, és egyes csőkötések annyira korrodálódtak, hogy valójában lyukak voltak rajtuk.Körülbelül 8,5 mm vastag, 3%-os krómacél kevesebb mint 8 hónap alatt szétesett.A fő korrózió a kút felső szakaszán történt, a kútfejtől lefelé körülbelül 380 méteres MD-ig, és a legrosszabbul korrodált csőkötések körülbelül 350 méteres MD körül voltak.Ez alatt a mélység alatt alig vagy egyáltalán nem figyeltek meg korróziót, de sok törmeléket találtak a csövek külső felületén.
A 9-5/8"-es burkolatot szintén levágták és kihúzták, és hasonló hatásokat figyeltek meg;korrózióval a kút felső szakaszán csak az egyik oldalon.Az indukált szivárgást a burkolat meggyengült részének szétrepedése okozta.
A vegyi injekciós vezeték anyaga 825 ötvözet volt.
Kémiai végzettség
A kémiai tulajdonságok és a korrózióvizsgálatok fontos szempontok a vízkőgátlók minősítésében, és a tényleges vízkőgátlót több éve minősítették és használták felső és tenger alatti alkalmazásokban.A tényleges vegyszeres fúrólyuk alkalmazásának oka a környezeti tulajdonságok javulása volt a meglévő fúrólyuk vegyszer cseréje révén. A vízkőgátlót azonban csak környezeti felső és tengerfenék hőmérsékleten (4-20 ℃) használták.A kútba fecskendezve a vegyszer hőmérséklete akár 90 ℃ is lehetett, de ezen a hőmérsékleten nem végeztek további vizsgálatokat.
A kezdeti korróziós teszteket a vegyszerszállító végezte el, és az eredmények 2-4 mm/év szénacélt mutattak magas hőmérsékleten.Ebben a szakaszban minimálisan bevonták az üzemeltető anyagtechnikai kompetenciáját.Később az üzemeltető új teszteket végzett, amelyek kimutatták, hogy a vízkőgátló erősen korrozív a gyártócsövekben és a gyártási burkolatban lévő anyagokra nézve, és a korróziós sebesség meghaladja a 70 mm/év értéket.Az Alloy 825 vegyi injekciós vezeték anyagát az injektálás előtt nem tesztelték a vízkőgátlóval szemben.A kút hőmérséklete elérheti a 90 ℃-ot, és ilyen körülmények között megfelelő vizsgálatokat kellett volna elvégezni.
A vizsgálat azt is feltárta, hogy a vízkőgátló tömény oldat pH-ja <3,0 volt.A pH-t azonban nem mérték.Később a mért pH nagyon alacsony, 0-1 pH értéket mutatott.Ez szemlélteti a mérések és az anyagi megfontolások szükségességét a megadott pH-értékeken túl.
Az eredmények értelmezése
A befecskendező vezeték (3. ábra) úgy van kialakítva, hogy a vízkőgátló hidrosztatikus nyomását meghaladja a befecskendezési pontban lévő nyomásnál.Az inhibitort nagyobb nyomáson fecskendezik be, mint amilyen a fúrólyukba van.Ez U-cső hatást eredményez a kút lezárásakor.A szelep mindig nagyobb nyomással nyílik a befecskendező vezetékben, mint a kútban.Emiatt vákuum vagy párolgás léphet fel az injekciós vezetékben.A korrózió sebessége és a lyukképződés veszélye a gáz/folyadék átmeneti zónában a legnagyobb az oldószer elpárolgása miatt.A kuponokon végzett laboratóriumi kísérletek megerősítették ezt az elméletet.Azokban a kutakban, ahol szivárgást tapasztaltak, a befecskendező vezetékeken lévő összes lyuk a vegyszerinjektáló vezeték felső részén volt.
A 4. ábra a DHC I vonal fényképezését mutatja jelentős lyukkorrózióval.A külső gyártócsövön látható korrózió a vízkőgátló lokális expozícióját jelezte a lyukasztási szivárgási ponttól.A szivárgást az erősen korrozív vegyszer okozta pontkorrózió és a vegyszerinjektáló vezetéken keresztül a gyártóházba való szivárgás okozta.A vízkőgátlót a gödrös kapilláris vezetékről a burkolatra és a csőre permetezték, és szivárgás történt.Nem vették figyelembe a befecskendező vezeték szivárgásának másodlagos következményeit.Arra a következtetésre jutottak, hogy a burkolat és a csövek korróziója annak a következménye, hogy koncentrált vízkőgátlók csapódtak le a kapilláris vonalról a burkolatra és a csőre, 5. ábra.
Ebben az esetben hiányzott az anyagkompetenciával foglalkozó mérnökök bevonása.A vegyi anyag korrozivitását a DHCI vonalon nem vizsgálták, és a szivárgásból eredő másodlagos hatásokat nem értékelték;például, hogy a környező anyagok elviselik-e a vegyi expozíciót.
A vegyifegyver-király esettörténete
Az események sorrendje
A HP HT mező vízkő-megelőzési stratégiája a vízkőgátló folyamatos befecskendezése volt a mélyedés biztonsági szelepe előtt.A kútban súlyos kalcium-karbonát-lerakódási potenciált azonosítottak.Az egyik kihívás a magas hőmérséklet, valamint a magas gáz- és kondenzátumtermelés, valamint az alacsony víztermelési sebesség volt.A vízkőgátló befecskendezésével az aggodalomra ad okot, hogy az oldószert a nagy gáztermelési sebesség eltávolítja, és a vegyszer pisztolykirálya a kút biztonsági szelepe előtti befecskendezési pontban fordul elő, 1. ábra.
A vízkőgátló minősítése során a hangsúly a termék HP HT-körülmények melletti hatékonyságán volt, beleértve a felső oldali folyamatrendszerben való viselkedést (alacsony hőmérséklet).A fő gondot magának a vízkőgátlónak a nagy gázsebesség miatti kicsapódása jelentette a gyártócsőben.A laboratóriumi vizsgálatok azt mutatták, hogy a vízkőgátló kicsapódhat és hozzátapadhat a cső falához.A biztonsági szelep működtetése ezért meghaladhatja a kockázatot.
A tapasztalatok azt mutatják, hogy néhány hetes működés után a vegyszervezeték szivárog.A fúrólyuk nyomását a kapilláris vezetékbe szerelt felületmérőn lehetett nyomon követni.A vonalat izoláltuk a kút integritásának elérése érdekében.
A vegyszerbefecskendező vezetéket kihúzták a kútból, kinyitották és megvizsgálták a probléma diagnosztizálása és a hiba lehetséges okainak feltárása érdekében.Amint a 6. ábrán látható, jelentős mennyiségű csapadékot találtunk, és a kémiai analízis kimutatta, hogy ennek egy része a lerakódásgátló.A csapadék a tömítésnél volt, a tömítést és a szelepet nem lehetett működtetni.
A szelep meghibásodását a szeleprendszer belsejében lévő törmelék okozta, amely megakadályozta, hogy a visszacsapó szelepek a fém-fém ülékbe essenek.A törmeléket megvizsgálták, és a fő részecskék fémforgácsnak bizonyultak, amelyek valószínűleg a kapilláris vezeték beépítése során keletkeztek.Ezenkívül fehér törmeléket azonosítottak mindkét visszacsapó szelepen, különösen a szelepek hátoldalán.Ez az alacsony nyomású oldal, azaz az oldal mindig érintkezik a fúrólyuk folyadékaival.Kezdetben úgy gondolták, hogy ez a termelő fúrásból származó törmelék, mivel a szelepek nyitva voltak, és ki voltak téve a fúrólyuk folyadékának.De a vizsgálat során a törmelék olyan polimernek bizonyult, amely hasonló kémiai összetételű, mint a vízkőgátlóként használt vegyszer.Ez felkeltette érdeklődésünket, és a Statoil fel akarta tárni a kapillárisvezetékben jelen lévő polimer törmelék okait.
Kémiai végzettség
A HP HT területén számos kihívást jelent a megfelelő vegyszerek kiválasztása a különféle gyártási problémák enyhítésére.A vízkőgátló folyamatos injektáló fúrólyuk minősítésénél a következő vizsgálatokat végeztük el:
● A termék stabilitása
● Termikus öregedés
● Dinamikus teljesítménytesztek
● Kompatibilitás a formációs víz és hidrát inhibitorral (MEG)
● Statikus és dinamikus pisztolykirály teszt
● Újraoldódási információ víz, friss vegyszer és MEG
A vegyszert előre meghatározott adagolási sebességgel fecskendezik be,de a víztermelés nem feltétlenül lesz állandó,azaz vízcsomózás.A vízi csigák között,amikor a vegyszer bejut a fúrólyukba,egy meleg fogadja majd,gyorsan áramló szénhidrogén gázáram.Ez hasonló a vízkőgátló befecskendezéséhez gázemelő alkalmazásban (Fleming etal. 2003).
a magas gázhőmérséklet,az oldószer eltávolításának veszélye rendkívül magas, és a pisztolykirály a befecskendező szelep eltömődését okozhatja.Ez még a magas forráspontú/alacsony gőznyomású oldószerekkel és egyéb gőznyomáscsökkentő anyagokkal (VPD-kkel) összeállított vegyszerek esetében is fennáll. Részleges eltömődés esetén,formáció víz áramlása,A MEG-nek és/vagy a friss vegyszernek képesnek kell lennie arra, hogy eltávolítsa vagy újra feloldja a kiszáradt vagy kiszáradt vegyszert.
Ebben az esetben egy új laboratóriumi tesztberendezést terveztek, hogy megismételje az áramlási körülményeket a befecskendező nyílások közelében egy HP/HTg gyártási rendszerben.A dinamikus pisztolykirály tesztek eredményei azt mutatják, hogy a javasolt alkalmazási körülmények között jelentős oldószerveszteséget regisztráltak.Ez gyors fegyverkirályhoz és az áramlási vonalak esetleges blokkolásához vezethet.A munka tehát bebizonyította, hogy viszonylag jelentős kockázatot jelent a folyamatos vegyszerinjektálás ezekben a kutakban a víztermelés előtt, és elhatározták, hogy ezen a területen módosítják a szokásos indítási eljárásokat, elhalasztva a vegyszerinjektálást a víz áttörésének észleléséig.
A vízkőgátló folyamatos befecskendezési fúrólyukhoz való minősítése nagy hangsúlyt fektet az oldószer eltávolítására és a vízkőgátló pisztolykirályára a befecskendezési pontban és az áramlási vonalban, de magában a befecskendező szelepben nem értékelték a pisztolykirály lehetőségét.A befecskendező szelep valószínűleg meghibásodott a jelentős oldószerveszteség és a gyors pisztolykirály miatt,6. ábra. Az eredmények azt mutatják, hogy fontos a rendszer holisztikus képe;nem csak a termelési kihívásokra összpontosít,hanem a vegyszer befecskendezésével kapcsolatos kihívások is,azaz befecskendező szelep.
Más területekről szerzett tapasztalat
Az egyik korai jelentés a nagy távolságú vegyszer-befecskendező vezetékekkel kapcsolatos problémákról a Gull fak sandVig dis műholdmezőkből származott (Osa etal.2001). a vezetékbe a befecskendező szelepen keresztül.Új irányelveket dolgoztak ki a tenger alatti termelési vegyszerek fejlesztésére vonatkozóan.A követelmények magukban foglalták a részecskék eltávolítását (szűrését) és a hidrát inhibitor (pl. glikol) hozzáadását az összes vízbázisú vízkőgátlóhoz, amelyet a tenger alatti sablonokhoz kell befecskendezni.Kémiai stabilitás,a viszkozitást és a kompatibilitást (folyadék és anyagok) is figyelembe vettük.Ezek a követelmények tovább kerültek a Statoil rendszerébe, és magukban foglalják a fúrólyukba történő vegyszerinjektálást.
Az Oseberg S vagy mező fejlesztési szakaszában úgy döntöttek, hogy minden kutat DHC I rendszerrel kell kiegészíteni (Fleming etal. 2006). A cél a CaCO megelőzése volt.;pikkelyképződés a felső csőben SI injekcióval.A vegyszerinjektáló vezetékekkel kapcsolatban az egyik legnagyobb kihívás a felület és a fúrólyuk kimenet közötti kommunikáció megteremtése volt.A vegyszerinjektáló vezeték belső átmérője 7 mm-ről 0,7 mm-re (ID) szűkült a gyűrűs biztonsági szelep körül a hely korlátai miatt, és a folyadék ezen a szakaszon keresztül történő szállítási képessége befolyásolta a sikerességi arányt.Több platform kútjában vegyszerbefecskendező vezetékek voltak eltömve,de az okot nem értették.Különféle folyadékok (glikol,nyers,kondenzátum,xilol,vízkő gátló,víz stb.) laboratóriumi vizsgálatnak vetették alá a viszkozitást és a kompatibilitást, és előre és fordított áramlásban pumpálták a vezetékek kinyitásához;azonban,a cél vízkőgátlót nem lehetett egészen a vegyszerbefecskendező szelepig lepumpálni.További,szövődményeket észleltek a foszfonát lerakódásgátló kicsapódása, valamint a maradék CaCl z befejező sóoldat egy kútban, és a vízkőgátló pisztolykirálya egy magas gázolajarányú és alacsony vízlevágású kútban (Fleming etal.2006)
Tanulságok
Tesztmódszer fejlesztés
A DHC I rendszerek meghibásodásából levont fő tanulságok a vízkőgátló műszaki hatékonyságára vonatkoztak, nem pedig a funkcionalitásra és a vegyszerinjektálásra.A felső oldali befecskendezés és a tenger alatti befecskendezés a túlórán túl jól működött;azonban,a kérelmet kiterjesztették a fúrólyukba történő vegyszerinjektálásra a vegyszerminősítési módszerek megfelelő frissítése nélkül.A Statoil tapasztalata a bemutatott két helyszíni esetből az, hogy a vegyi anyagok minősítésére vonatkozó irányadó dokumentációt vagy irányelveket frissíteni kell, hogy az tartalmazza az ilyen típusú vegyi alkalmazásokat.A két fő kihívást az alábbiakban határozták meg: i) a vegyszerinjektáló vezetékben kialakuló vákuum és ii) a vegyszer potenciális kicsapódása.
A vegyszer elpárologhat a gyártó csövön (amint az a pisztolykirály toknál látható) és a befecskendező csőben (a vákuumházban átmeneti interfész került azonosításra), fennáll annak a veszélye, hogy ezek a csapadékok az áramlással együtt mozognak, és a befecskendező szelepbe és tovább a kútba.A befecskendező szelepet gyakran a befecskendezési pont előtti szűrővel tervezik,ez kihívás,mivel csapadék esetén ez a szűrő eltömődhet, ami a szelep meghibásodását okozza.
A megfigyelések és a levont tanulságok előzetes következtetései a jelenségek kiterjedt laboratóriumi vizsgálatát eredményezték.Az átfogó cél az volt, hogy új minősítési módszereket dolgozzanak ki, hogy a jövőben elkerüljék a hasonló problémákat.Ebben a tanulmányban különféle vizsgálatokat végeztek, és számos laboratóriumi módszert terveztek (fejlesztettek ki) a vegyi anyagok vizsgálatára az azonosított kihívások tekintetében.
● Szűrődugulások és termékstabilitás zárt rendszerekben.
● A részleges oldószerveszteség hatása a vegyszerek korrozivitására.
● A kapillárison belüli részleges oldószerveszteség hatása szilárd anyagok vagy viszkózus dugók képződésére.
A laboratóriumi módszerek tesztelése során számos lehetséges problémát azonosítottak
● Ismétlődő szűrőeltömődések és rossz stabilitás.
● Szilárdanyag képződés a kapillárisból történő részleges elpárolgás után
● A pH változása az oldószerveszteség miatt.
Az elvégzett tesztek jellege további információkat és ismereteket is szolgáltatott a kapillárisokban lévő vegyi anyagok fizikai tulajdonságainak változásaival kapcsolatban, ha bizonyos feltételeknek vannak kitéve.,és ez miben különbözik a hasonló feltételeknek alávetett tömeges megoldásoktól.A vizsgálati munka jelentős különbségeket is azonosított az ömlesztett folyadék között,gőzfázisok és maradék folyadékok, amelyek megnövekedett csapadéklehetőséget és/vagy fokozott korróziót okozhatnak.
A vízkőgátlók korróziós hatásának vizsgálati eljárását kidolgozták, és belefoglalták az irányadó dokumentációba.Minden alkalmazáshoz kiterjesztett korróziós vizsgálatot kellett végezni a vízkőgátló befecskendezése előtt.A befecskendező vezetékben lévő vegyi anyag pisztolykirályi tesztjeit is elvégezték.
A vegyi anyag minősítésének megkezdése előtt fontos egy olyan munkakör kialakítása, amely leírja a vegyszer kihívásait és célját.A kezdeti szakaszban fontos azonosítani a fő kihívásokat, hogy ki lehessen választani a problémát megoldó vegyi anyagok típusát.A legfontosabb elfogadási kritériumok összefoglalása a 2. táblázatban található.
Vegyszerek minősítése
A vegyi anyagok minősítése az egyes alkalmazások vizsgálatából és elméleti értékeléséből áll.Meg kell határozni és meg kell határozni a műszaki specifikációt és a vizsgálati kritériumokat,például az EBK-n belül,anyag kompatibilitás,a termék stabilitása és a termék minősége (részecskék).További,a fagyáspont,viszkozitás és kompatibilitás más vegyszerekkel,hidrát inhibitor,meg kell határozni a képződményvizet és a keletkezett folyadékot.A vegyi anyagok minősítésére használható vizsgálati módszerek egyszerűsített listája a 2. táblázatban található.
Folyamatos összpontosítás és figyelemmel kísérés a műszaki hatékonyságra,az adagolási arányok és a HSE tények fontosak.A termék követelményei megváltoztathatják a szántóföld vagy a feldolgozó üzem élettartamát;a termelési sebességtől és a folyadék összetételétől függően változhat.Nyomon követési tevékenység a teljesítmény értékelésével,Az optimális kezelési program biztosítása érdekében gyakran kell optimalizálni és/vagy új vegyszereket tesztelni.
Az olaj minőségétől függően,víztermelés és műszaki kihívások az offshore termelő üzemben,a gyártási vegyszerek használata szükséges lehet az exportminőség eléréséhez,szabályozási követelmények,és a tengeri létesítmény biztonságos üzemeltetése.Minden területen más kihívások vannak, és a gyártáshoz szükséges vegyszerek mennyisége mezőnként és túlóránként változik.
Fontos, hogy a minősítési programban a gyártási vegyszerek műszaki hatékonyságára összpontosítsanak,de nagyon fontos a vegyszer tulajdonságaira is összpontosítani,mint például a stabilitás,a termék minősége és kompatibilitása.A kompatibilitás ebben a beállításban a folyadékokkal való kompatibilitást jelenti,anyagok és egyéb gyártási vegyszerek.Ez kihívás lehet.Nem kívánatos vegyszert használni egy probléma megoldására, hogy később kiderüljön, hogy a vegyi anyag hozzájárul vagy új kihívásokhoz vezet.Talán a vegyszer tulajdonságai és nem a technikai kihívás jelentik a legnagyobb kihívást.
Speciális követelmények
A szállított termékek szűrésére vonatkozó különleges követelményeket kell alkalmazni a tenger alatti rendszerre és a folyamatos befecskendezési mélyedésekre.A vegyszerbefecskendező rendszerben szűrőket és szűrőket kell biztosítani a felső oldali befecskendező rendszer utáni berendezés specifikációi alapján,szivattyúk és befecskendező szelepek,a mélyedésbefecskendező szelepekhez.Ha a vegyszerek fúrólyukba történő folyamatos befecskendezését alkalmazzák, a vegyszerinjektáló rendszer specifikációjának a legmagasabb kritikusságú specifikáción kell alapulnia.Ez lehet a szűrő a befecskendező szelep furatánál.
Injekciós kihívások
A befecskendező rendszer 3-50 km távolságot jelenthet a köldök alatti áramlási vonaltól és 1-3 km-es távolságot a kútba.Fontosak az olyan fizikai tulajdonságok, mint a viszkozitás és a vegyszerek szivattyúzásának képessége.Ha a viszkozitás a tengerfenék hőmérsékletén túl magas, akkor kihívást jelenthet a vegyszer pumpálása a vegyszerinjektáló vezetéken keresztül a tenger alatti köldökcsonkban és a tenger alatti befecskendezési pontig vagy a kútba.A viszkozitásnak meg kell felelnie a rendszer specifikációjának a várható tárolási vagy üzemi hőmérsékleten.Ezt minden esetben értékelni kell,és rendszerfüggő lesz.A vegyszerinjektálás sebessége a táblázat szerint a vegyszerinjektálás sikerének tényezője.A vegyszerinjektáló vezeték eltömődésének kockázatának minimalizálása érdekében,a vegyszereket ebben a rendszerben gátolni kell (ha lehetséges a hidrát).El kell végezni a kompatibilitást a rendszerben lévő folyadékokkal (konzerváló folyadék) és a hidrát inhibitorral.A vegyi anyag stabilitási vizsgálata tényleges hőmérsékleten (a lehető legalacsonyabb környezeti hőmérsékleten,környezeti hőmérséklet,tenger alatti hőmérséklet,befecskendezési hőmérséklet) át kell lépni.
A vegyszerinjektáló vezetékek adott gyakoriságú mosására szolgáló programot is mérlegelni kell.Megelőző hatást fejthet ki a vegyszerinjekciós vezeték rendszeres oldószeres átöblítése,glikolt vagy tisztítószert, hogy eltávolítsa az esetleges lerakódásokat, mielőtt azok felhalmozódnának, és a vezeték eltömődését okozhatják.Az öblítőfolyadék választott kémiai oldatának kell lenniekompatibilis az injekciós vezetékben lévő vegyszerrel.
Egyes esetekben a vegyszerinjektáló vezetéket többféle vegyi alkalmazáshoz használják, a terepi élettartam és a folyadékviszonyok különböző kihívásai alapján.A víz áttörése előtti kezdeti termelési szakaszban a fő kihívások eltérhetnek a késői életszakaszban tapasztaltaktól, amelyek gyakran a megnövekedett víztermeléshez kapcsolódnak.A nem vizes, oldószer alapú inhibitorról, például az aszfaltén-inhibitorról a vízbázisú vegyszerre, például a vízkőgátlóra való átállás kihívást jelenthet a kompatibilitás terén.Ezért fontos a távtartók kompatibilitására, minősítésére és felhasználására összpontosítani, amikor a vegyszerinjektáló vezetékben vegyi anyagcserét terveznek.
Anyagok
Anyagkompatibilitás tekintetében,minden vegyszernek kompatibilisnek kell lennie a tömítésekkel,elasztomerek,a vegyszerinjektáló rendszerben és a gyártóüzemben használt tömítések és építőanyagok.Ki kell dolgozni a vegyszerek (pl. savas vízkőgátló) korróziós hatásának vizsgálati eljárását folyamatos injektáló fúrólyuk esetén.Minden alkalmazáshoz kiterjesztett korróziós vizsgálatot kell végezni, mielőtt a vegyi anyagok befecskendezhetők.
Vita
Fel kell mérni a folyamatos fúrólyuk vegyszer-injektálás előnyeit és hátrányait.A vízkőgátló folyamatos befecskendezése a DHS védelmére A gyártócső egy elegáns módszer a kút vízkő elleni védelmére.Amint azt ebben a cikkben említettük, a fúrólyukba történő folyamatos vegyszerinjektálás számos kihívást jelent,a kockázat csökkentése érdekében azonban fontos megérteni a megoldáshoz kapcsolódó jelenségeket.
A kockázat csökkentésének egyik módja a vizsgálati módszerek fejlesztésére való összpontosítás.A felszíni vagy tenger alatti vegyszerinjektáláshoz képest eltérő és súlyosabb körülmények vannak lent a kútban.A vegyszerek fúrólyukba történő folyamatos befecskendezésére vonatkozó vegyszerek minősítési eljárásának figyelembe kell vennie ezeket a körülmények változásait.A vegyszerek minősítését aszerint kell elvégezni, hogy a vegyszerek milyen anyaggal érintkezhetnek.A kompatibilitás minősítésére és tesztelésére vonatkozó követelményeket olyan körülmények között, amelyek a lehető legközelebb reprodukálják a különböző kútéletciklus-feltételeket, amelyek között ezek a rendszerek működni fognak, frissíteni és be kell vezetni.A vizsgálati módszerek fejlesztését tovább kell fejleszteni a valósághűbb és reprezentatívabb tesztek érdekében.
Továbbá,a vegyszerek és a berendezés közötti kölcsönhatás elengedhetetlen a sikerhez.A befecskendező vegyszerszelepek fejlesztésénél figyelembe kell venni a kémiai tulajdonságokat és a befecskendező szelep elhelyezkedését a kútban.Megfontolandó a valódi befecskendező szelepek vizsgálata a vizsgálóberendezés részeként, valamint a vízkőgátló és a szelepkonstrukció teljesítményvizsgálatának elvégzése a minősítési program részeként.A vízkőgátlók minősítésére,a fő hangsúly korábban a folyamat kihívásaira és a léptékgátlásra irányult,de a jó skála gátlás a stabil és folyamatos injekciótól függ.Stabil és folyamatos befecskendezés nélkül megnő a lerakódási lehetőség.Ha a vízkőgátló befecskendező szelep el van nyomva, és nincs vízkőgátló injekció a folyadékáramba,a kút és a biztonsági szelepek nincsenek védve a vízkőtől, így a biztonságos termelés veszélybe kerülhet.A minősítési eljárásnak az eljárási kihívásokon és a minősített vízkőgátló hatékonyságán túl a vízkőgátló befecskendezésével kapcsolatos kihívásokról is gondoskodnia kell.
Az új megközelítés több tudományágat is magában foglal, és tisztázni kell a szakterületek közötti együttműködést és a felelősségi köröket.Ebben az alkalmazásban a felső folyamatrendszer,tenger alatti sablonok, kutak tervezése és befejezése.A több tudományágat átfogó hálózatok, amelyek a vegyszerinjektáló rendszerek robusztus megoldásainak kifejlesztésére összpontosítanak, fontosak, és talán a sikerhez vezető út.A különböző tudományágak közötti kommunikáció kritikus;különösen fontos a szoros kommunikáció az alkalmazott vegyszereket felügyelő vegyészek és a kútban használt berendezéseket felügyelő kútmérnökök között.A különböző tudományágak kihívásainak megértése és az egymástól való tanulás elengedhetetlen az egész folyamat összetettségének megértéséhez.
Következtetés
● A vízkőgátló folyamatos befecskendezése a DHS védelmére
● Az azonosított kihívások megoldása,a következő ajánlások:
● Egy dedikált DHCI minősítési eljárást kell végrehajtani.
● A vegyszerbefecskendező szelepek minősítési módszere
● Kémiai funkcionalitás vizsgálati és minősítési módszerei
● Módszerfejlesztés
● Releváns anyagvizsgálat
● A multidiszciplináris interakció, ahol a különböző érintett tudományágak közötti kommunikáció kulcsfontosságú a sikerhez.
Köszönetnyilvánítás
A szerző köszönetet mond a Statoil AS A-nak, hogy engedélyezte ennek a munkának a közzétételét, valamint Baker Hughesnek és Schlumbergernek, hogy engedélyezték a 2. ábrán látható kép használatát.
Elnevezéstan
(Ba/Sr)SO4=bárium/stroncium-szulfát
CaCO3 = kalcium-karbonát
DHCI = fúrólyukú vegyszerinjektálás
DHSV=furat biztonsági szelep
eg=például
GOR=gázolaj arány
HSE = egészségbiztonsági környezet
HPHT = magas nyomású magas hőmérséklet
ID = belső átmérő
ie=azaz
km=kilométer
mm = milliméter
MEG = monoetilénglikol
mMD = méteres mért mélység
OD = külső átmérő
SI = skála inhibitor
mTV D = méter teljes függőleges mélység
U-cső=U alakú cső
VPD = gőznyomás-csökkentő
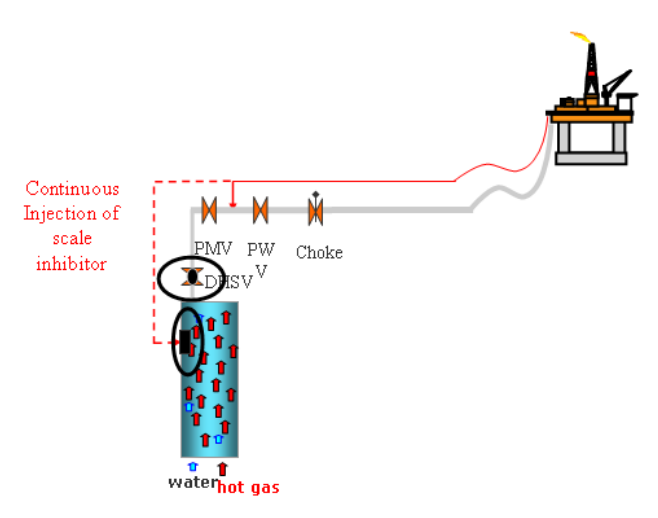
1. ábra: A tenger alatti és mélyedéses vegyszerinjektáló rendszerek áttekintése atipikus területen.Vázlat a vegyszerinjektálásról az upstream DHSV-ről és a kapcsolódó várható kihívásokról.DHS V = fúrólyuk biztonsági szelep, PWV = folyamatszárnyas szelep és PM V = folyamat főszelep.
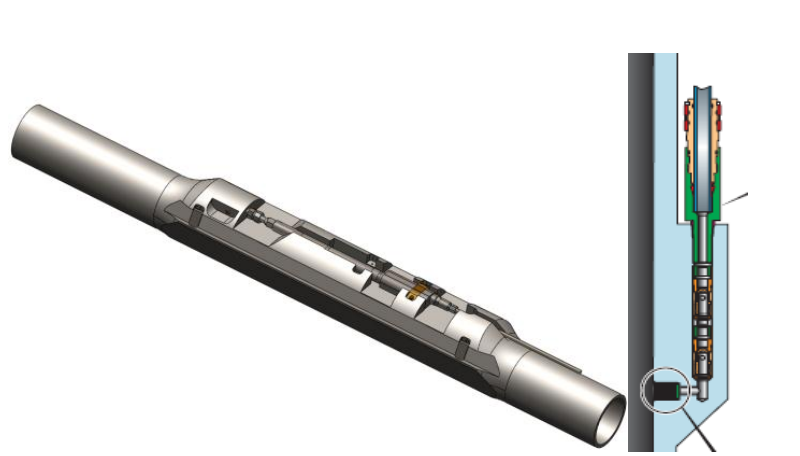
2. ábra Az atipikus fúrólyuk vegyszer-befecskendező rendszer vázlata a tüskével és a szeleppel.A rendszert a felületi elosztóhoz csatlakoztatják, átvezetik és csatlakoztatják a cső gyűrűs oldalán lévő csőakasztóhoz.A vegyszerinjektáló tüskét hagyományosan a kút mélyére helyezik, vegyi védelem céljából.
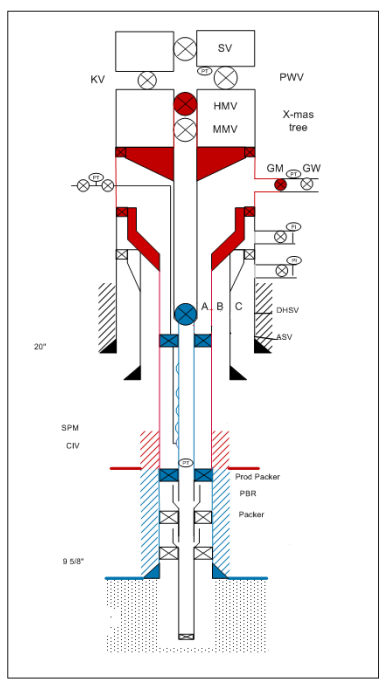
3. ábra Tipikus kútgát vázlata,ahol a kék szín az elsődleges kútzáró burkolatot jelöli;ebben az esetben a gyártócső.A piros szín a másodlagos gátburkot jelöli;a burkolat.A bal oldalon a vegyszerinjektálás látható, fekete vonal injektálási ponttal a gyártócsőhöz a pirossal jelölt területen (másodlagos gát).
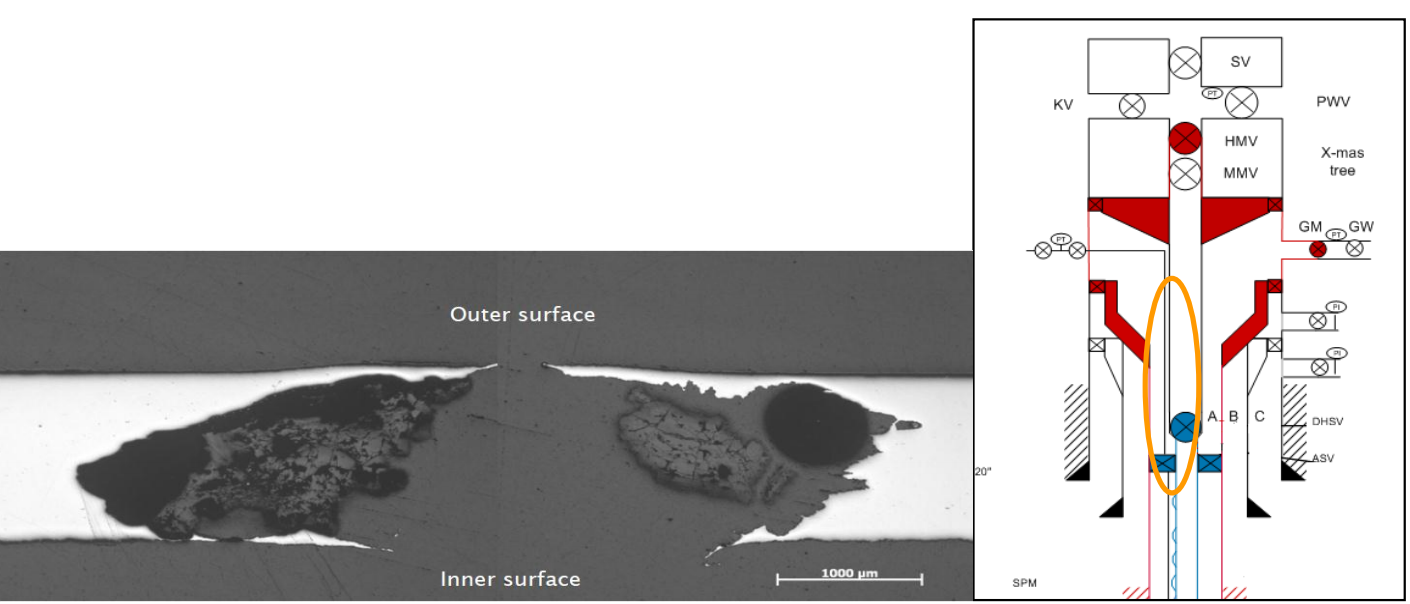
4. ábra: A 3/8”-os befecskendező vezeték felső részén található lyuk.A területet a narancssárga ellipszissel jelölt atipikus kútgát sematikus vázlata mutatja.
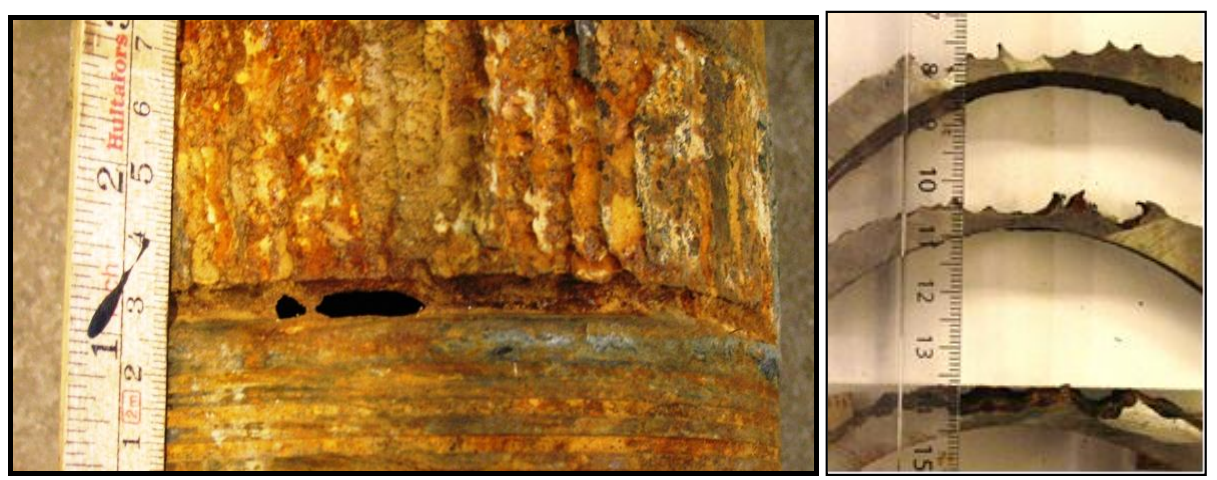
5. ábra: Erős korróziós támadás a 7”-os 3%-os króm csövön.Az ábra a korróziós támadást mutatja a kátyús vegyszer-injektáló vezetékről a gyártócsőre permetezett vízkőgátló után.
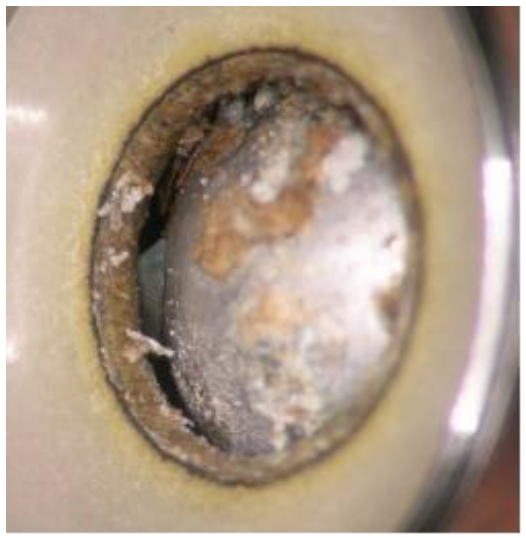
6. ábra: A vegyszerbefecskendező szelepben talált törmelék.A törmelék ebben az esetben valószínűleg a telepítési folyamatból származó fémforgács volt, valamint néhány fehéres törmelék.A fehér törmelék vizsgálata a beinjektált vegyszerhez hasonló kémiájú polimereknek bizonyult
Feladás időpontja: 2022.04.27